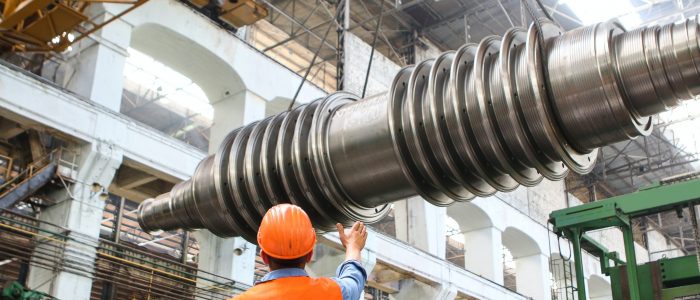
Does Britain make anything, anymore?
29.September.2020
Does Britain make anything, anymore?
All our manufacturing has gone to China. That’s the most common narrative when conversation turns to the state of British industry. We might have led the Industrial Revolution, but we’re not a country that likes to get its hands dirty and make things anymore. Stand-offs with the unions, high labour costs, slipping productivity, lack of government support – the story continues to be told of Britain’s slow cycle of decline.
However, if you look at the numbers the country is far from being the poor man of the post-industrial era. Britain’s manufacturing currently ranks 9th in the world and, according to the ONS, has grown 1.4% every year since 1948. Yes, there was a decline in manufacturing in the 1970 and 80s. For example, British car production fell from a peak of two million in the early 70s to just one million in 1983. But the country has bounced back and by the late 1990s it was back at two million.
Today, the automotive sector is a British success story. Although we manufacture German and Japanese brands, the British auto industry employs 169,000 people and supports a further 78,000 jobs. Up to 25,000 new jobs could be created with the advent of connected and autonomous cars, and British factories are already producing components for the electric vehicle market.
Currently, the UK has six design centres, eight major premium and sports car manufacturers, five commercial vehicle, nine engine, nine bus and coach, over 60 specialist car and six mainstream car manufacturers. There are 2,500 companies in the supply chain and 20 R&D centres according to The Society of Motor Manufacturers and Traders. Currently, 80% of a vehicle can be manufactured in the UK and the industry has an annual turnover of £71.6 billion and accounts for 12% of the UK’s total exports.
UK remains a global leader in aerospace as well, with 128,000 direct jobs and 140,000 indirect jobs supported across this industry. It has an annual turnover of £31 billion and with the introduction of hybrid and electric-powered aircraft, there will be a huge opportunity for Britain to export to countries with no manufacturing base in aerospace. The UK currently has an 18% share of the global market making it number one in Europe and second only to the US worldwide.
Automotive and aerospace alone demonstrate that the UK still has a vibrant manufacturing base and that not everything is made in China. Defence, pharmaceuticals, plastics, electronics, nuclear energy – Britain is a powerhouse in all of these fields and more. In total, British manufacturing employs 2.6 million people and accounts for 44% of UK exports.
Looking ahead, there is the potential for manufacturing to become an even more important part of the British economy in the post-COVID, post-Brexit world. Even with these challenges, British industry is far from being in terminal decline and with a coordinated strategy in the coming years the country might be able to climb back up the international rankings.
Five action points for British manufacturing
New technology
Digitisation has swept through manufacturing operations around the world. It’s often referred to as the fourth industrial revolution, or Industry 4.0. Smart factories are equipped with three key forms of technology that are revolutionising manufacturing: automated machinery; sensors to monitor output and quality assurance; and artificial intelligence and machine learning capable of predicting and averting bottlenecks and breakdowns.
British manufacturing needs to adopt these technologies at a greater rate in order to improve productivity and competitiveness. Cost is one reason for the reluctance to do so. Another is the fear that robots will take people’s jobs. That perception needs to change. Smart factories can’t function without people employed in high value, highly skilled roles. To an extent, the Brexit debate has distracted British manufacturing from the pressing issue of equipping our factories for the future and it’s something we need to focus on going forwards.
Finance
Britain’s strength in design and innovation, widely championed in recent decades, needs to be coupled with more strategic investment across the manufacturing sector. Adoption of the technology and a move to the Industry 4.0 model described above will require bold investment by firms and may also require government support.
However, even where finance is available, there has been a reluctance to invest for two reasons. Firstly, firms in the sector are unsure which technologies to opt for. Secondly, there is a widespread a lack of confidence in the future of the industry. For some, the credit crunch of 2008, Brexit and the impact of COVID-19 look like just the latest points on the timeline of Britain’s perceived industrial decline.
New business models
Perhaps the issues British manufacturing faces in relation to finance and technology can be ameliorated through wider adoption of the servitisation business model. As consumers, we are already familiar with how it works. Instead of buying a new iPhone, you go onto Apple’s plan, pay a monthly fee, and when the latest model arrives you hand in your old smartphone and start using a new one. It is becoming possible for firms to do the same thing with the machinery they use and the software that runs it.
The equipment is owned, installed, monitored and maintained by the company that made it. The factory using the machinery only pays for it while it’s running, or according to its output. With servitisation, machinery moves from the assets column of the balance sheet to the expenses column in the accounts and concerns about finance, selecting the right technology and depreciation are relieved.
The home front
Britain is strong when it comes to manufacturing highly engineered products, as seen in the automotive and aerospace industries, for example. However, we’re not as good when it comes to making everyday items for the domestic market or export. An example to emulate is Numatic International in Somerset. Not only does it make the iconic Henry vacuum cleaner, it also manufactures and exports industrial cleaning equipment. While others in its category now use factories in the Far East, Numatic has steadily invested in its products, facilities and workforce in Britain. In 2019, profits were up 5.7% despite Brexit uncertainty.
British manufacturing would be in a healthier position if more of the products that are designed and developed in the UK were made here, leveraging our strength in innovation to boost manufacturing. It’s an area where strategic government support could see a strong return and, from an environmental perspective, locally made products have a lower carbon footprint.
Skills
Changing demographics are creating a skills crisis in British manufacturing. According to The Manufacturer’s most recent report on UK Manufacturing Statistics, older skilled workers are retiring and there simply aren’t enough young people with the right training to replace them.
One response has been for firms to establish their own training schemes and academies. While this is a viable solution for large companies, much of the UK manufacturing sector is made up of specialised SMEs that need skilled workers but can’t afford to train them. The government urgently needs to work with manufacturers and the education sector to vastly increase the numbers of young people leaving education with STEM and/or vocational qualifications suited to modern industry.